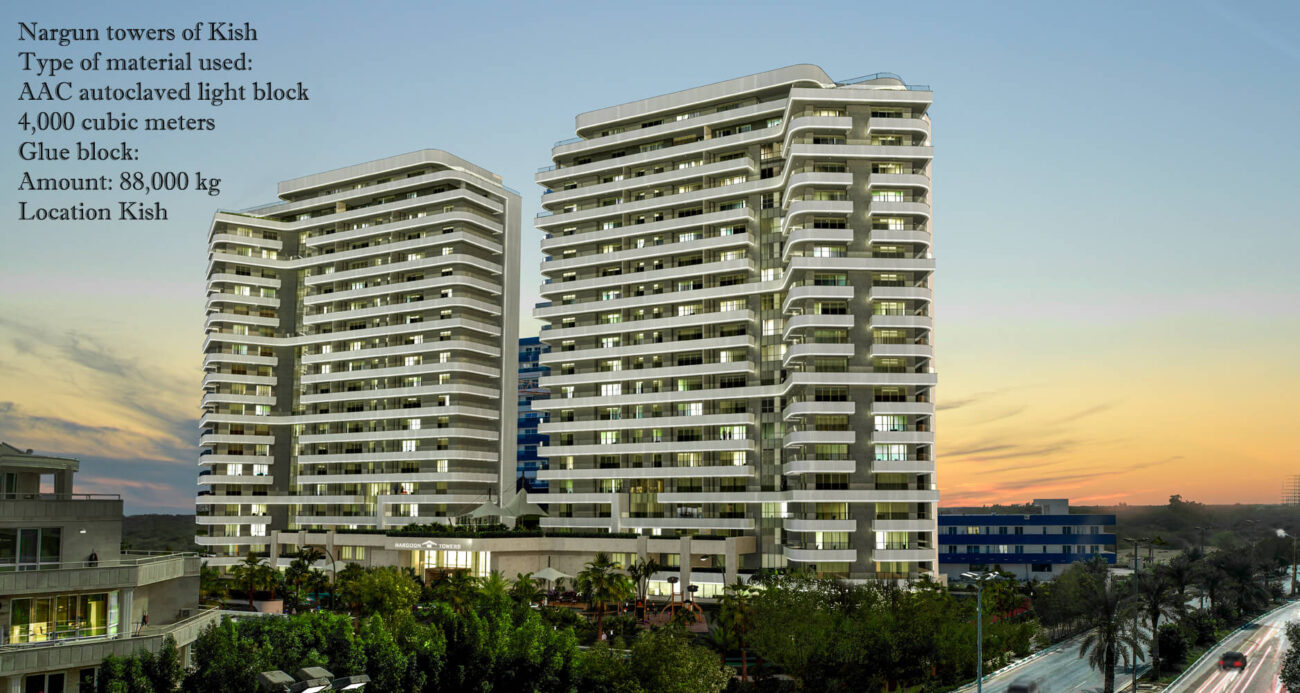
Introduction
With the expansion of the construction industry, the use of lightweight and durable materials in the production of structural and non-structural infill components has been taken into consideration. In this context, the technology of autoclaved aerated concrete or gas concrete, known by the acronym AAC, has been introduced. Aside from the manufacturing process, which offers remarkable speed and ease, a set of physical characteristics and the composition of these components make them some of the most commonly used elements. This has led to an increased interest in using these components in non-load-bearing and load-bearing non-structural elements.
AAC blocks are among the components whose applications are rapidly expanding. Additionally, the characteristics of these blocks, such as their compatibility with environmental conditions, stability and durability, lightweight, and performance features as thermal, fire, and sound insulation, make them a suitable alternative to conventional materials used in building structures. Furthermore, the ability to produce these blocks in various shapes, the ease of cutting these components, and their straightforward installation using available guidelines enhance their popularity.
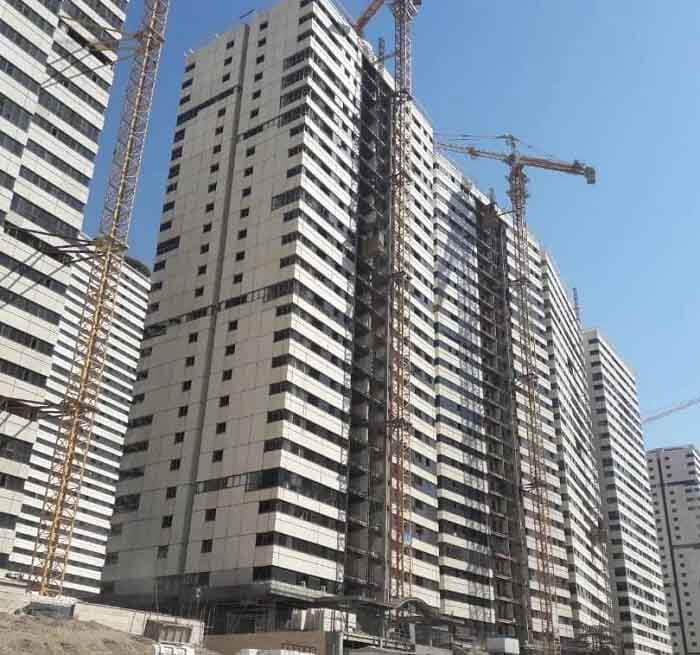
Scope of Application
Walls made from AAC blocks can be used as partition walls and exterior walls. Exterior walls are subjected to wind and earthquake loads and must be able to withstand impact loads, while partition walls are affected by earthquakes and need to be able to respond to smaller impact loads. Accordingly, the design and construction standards for these walls differ.
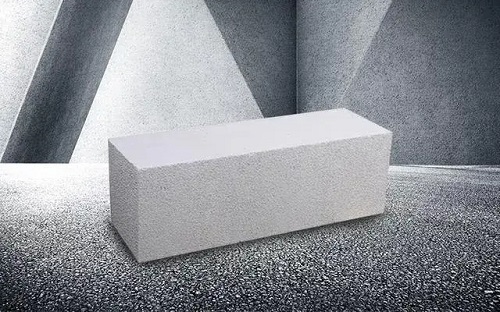
History
Autoclaved Aerated Concrete (AAC) is a type of lightweight concrete filled with closed-cell air bubbles, invented and produced for the first time in the 1920s by Dr. Johan Axel Eriksson, an assistant professor at Stockholm Institute of Technology in Sweden. The motivation behind its production was to protect forests and provide materials with wood-like properties such as lightness, thermal insulation, ease of cutting, and shaping while avoiding wood's downsides like flammability, decay, and damage from termites. Later, in 1945, as part of its development, German inventors discovered a method to cut it, leading to mass production, which was certified by the German standard (DIN) in 1958. After growing in Sweden during the 1950s, it was mass-produced by German and Polish companies, and from 1960 onward, due to its cost-effectiveness in construction, German scientists began to consider ways to strengthen it. In the course of this advancement, by 1977, these materials had been precision-cut into male and female shapes, minimizing construction issues. Starting in 1987, with the production of larger components, a revolution in construction took place, greatly reduced build times, and by 1994, thanks to new research and studies, the strength and lightness of this product reached perfection.
Today, this product is manufactured in many countries using various methods and different brand names. The products produced and offered under different brand names have differences in the proportions of raw material mixtures, cutting methods for the concrete, and stages of the production process.
1- Water + lime + silica + Cement
2- Add aluminum powder
3- ball mill
4- Mold or format
5- The volume of the cake increases 2to3 times, Release of hydrogen gas/Rest for 2 to 3 hours
6- Remove the cake from the mold and Moving the cake for cutting
7- High speed cutting vertically and horizontally
8- Cleaning the chips from cutting
9- Transfer to autoclave
10- steam cooking,12 bar pressure, The temperature is 180 degrees,10 to 12 hours
11- split
12- Transport for packing
13- Packing and loading
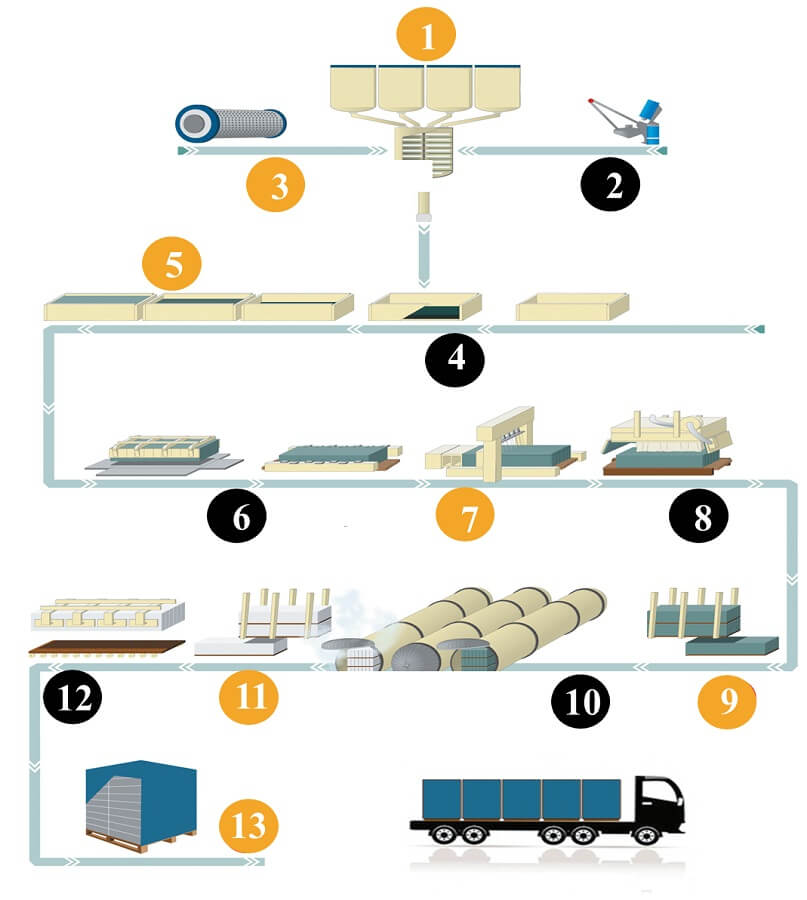
Conversion of limestone to quicklime
aO + CO2 = heat + CaCO3
Reaction of quicklime with water to form hydrated lime
CaO + H2O → Ca(OH)2 + heat
Reaction of hydrated lime with aluminium powder
2AL + Ca(OH)2 +6H2O → Ca[AL(OH)4]2 + 3H2
Porosity agent: 6H
Agent for concrete resistance: hydration of calcium silicate
mCaO.SiO2.nH2O m>2,n>6
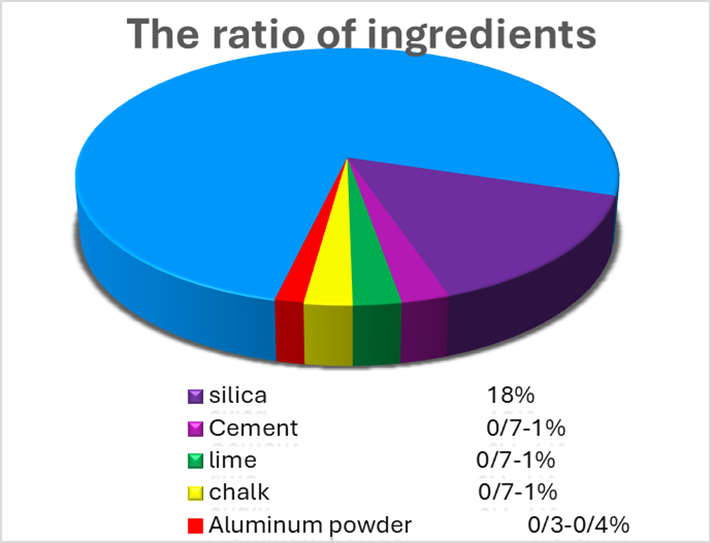
The steps of the AAC block production line
Processing and storage of sand/silica
Silica is one of the most important raw materials of AAC light concrete and it is prepared from internal mines, lime is also processed and baked inside the factory. In the light concrete production line, there are storage silos for raw materials, which are: silica silo, lime silo, and cement silo, and the raw materials are gradually entered into the production line after being stored in these silos. Silica, lime and cement are transported from the bottom of the silos by special elevators and enter the production line within a certain period of time.
In the first stage of lightweight concrete production, raw materials including silica and water are mixed in the mill as slurry or mud, and in the next mill, the materials used, including silica, lime and cement, are mixed dry after weighing, and in fact two mills This stage has mill No. 1 (wet material mill) and mill No. 2 (dry material), which after mixing and processing, the materials are transferred to the next stage. If the moisture content of these materials is not enough or if their mixture is dry, adding water is used to remove its dryness.
The last stage of mixing
At this stage, the most important thing is to mix these three materials in the form of slurry. Special mixers receive the mixture of the three main ingredients of AAC Block production.
These mixers are responsible for carefully checking the weight of the incoming product. The obtained product is transferred to the second stage for molding.
Before the materials are transferred to the molding part, they are carefully weighed and mixed in special mixers for a certain period of time. In this section, there are 3 types of raw materials in which the final weighing of the materials is done.
These mixers are responsible for carefully checking the weight of the incoming product. The obtained product is transferred to the next stage for molding.
Aluminum powder is added to the mixture and aeration begins;
In this step, aluminum powder is uniformly sprinkled on the light concrete obtained in the previous step. In this step, water is used again to completely combine the aluminum powder with the material mixture.
Before doing any other action, the desired composition is transferred to the laboratory and its quality is checked by experts. If there is the slightest problem in this combination or the percentage of the combined materials is not correct, the materials are returned to the previous steps.
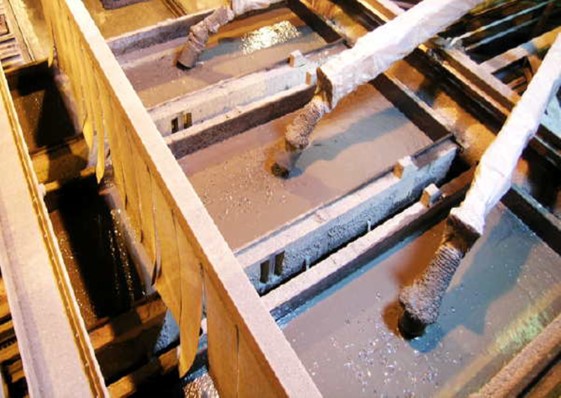
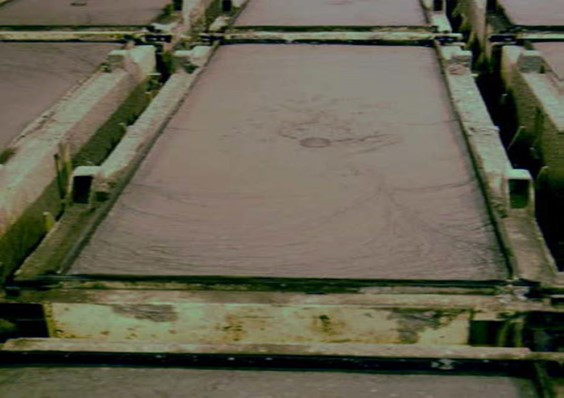
Attractive and wonderful features that are exclusive to AAC blocks.
1 -It increases the construction speed by 3 to 4 times ompared to normal materials.
2- It is cost-effective and also reduces steel consumption by more than 30%.
3-It is very light building reduces the static load of tall buildings and towers.
4- It is very light weight with a density of 450 to 550 kg/m2 (one third lighter than normal materials)
5- It reduces construction costs and saves time.
6- It does not need wall post.
7- Sound insulation exceeding 50 decibels.
8- Thermal and cooling insulation, significantly reducing energy consumption heating and cooling ompared to conventional building materials
9- Moisture insulation and freeze resistance.
10- Cost savings and ease of transportation due to the ability for palletized packaging.
11- Remarkably fast and easy installation owing to lightweight, precise sizing, impact resistance and screw-compatibility.
12- Easy cutting for carrying out electrical and plumbing installations.
13- A fire-resistant wall capable of withstanding direct fire up to 1200 degrees Celsius for 4 hours.
14- Reduction of earthquake forces due to low density, decreased dead load of the structure, and high compressive strength.
15- High safety and durability without the need for repairs.
16- Minimal finishing coverings for façades, leading to reduced plastering costs due to a smooth and level surface.
17- Increase in interior space of the building
18- Production capability based on client needs
19- No penetration of vermin
20- Recyclable and non-toxic
21- Environmentally friendly and compatible
22- Standard surface water absorption at the initial 1 centimetre, with proper adhesion of façade coverings
23- It does not submerge in water for up to 6 months
24- Resistant to loads caused by strong winds and storms
25- Known as lightweight concrete, composed of silica, cement, lime, aluminium powder, stone gypsum, and water.
26- Unlike conventional hollow materials, this material has a dense, porous, and white appearance.
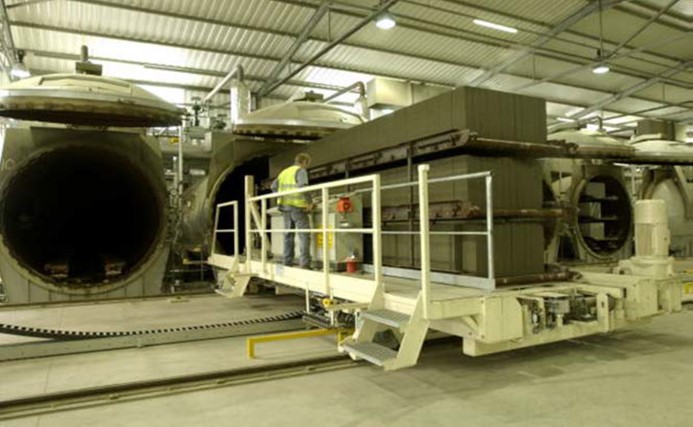
Lightweight concrete is processed in an autoclave
This process, which is called autoclaving of light concrete, is done in three stages:
First, the lightweight concrete is compressed under the pressure of 0.04 to 0.06 MPa by steam and its temperature is brought to 175 degrees Celsius.
In the next step of autoclaving, the pressure applied to the lightweight concrete in the machine reaches 0.8 to 1.2 MPa and it is subjected to these conditions for 5 to 7 hours.
The last stage of autoclaving is lowering the temperature of lightweight concrete.
During the three stages that lightweight concrete goes through in the autoclave, the temperature of the material reaches 200 degrees Celsius and the pressure reaches 12 atmospheres.
Opening the mold and turning the AAC cake
The molds are rotated 90 degrees, then the concrete is placed on the floor, that is, the side part of the mold is placed as the bottom of the mold.
After the molds are finished from the clamping stage, the rotating handle rotates the mold 90 degrees. This opens the handle of the mold and separates the body of the mold, so that the AAC cake remains on one side of the mold for cutting. This flipping system has proven to be the safest way to flip the cake in a vertical cutting position, as a AAC cake on the side of the mold for processing and cutting.
Collecting AAC molds and lubricating them
After the AAC mold is opened, it goes to the casting stage again, but before that, the molds are cleaned and special materials are sprinkled on them so that the material does not stick to the molds after pouring the AAC material. All cleaning and oiling steps can be done automatically.
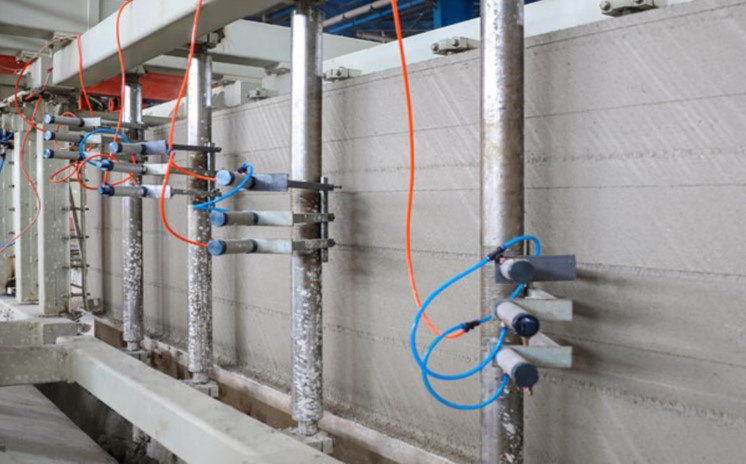
AAC block Cutting
Quality control in the third stage is the first word. Before entering the line, the final product is controlled by chemical tests to ensure that it is sufficiently ventilated. The outer surface of the is removed in this part of the factory to reveal a smooth and defined surface of the molds. In this part, the side walls transfer the molds to the cutting section.
The cutting machines cut lengthwise with the care of the staff. They adjust the longitudinal and transverse cutting sizes of the molds according to the customers' orders. The cutting size of can be adjusted and changed, and there is no need to worry about it. But it should not be lower than the standard that does not have the necessary efficiency. If it is more than one amount, the will take up a lot of space and will not meet the expectations of customers and consumers.
The machines are capable of vertical block cutting, horizontal cutting, thickness cutting and cutting for crotch and tongue or groove. There are different types of pneumatic wire cutting systems in specific capacities.
AAC block separation and autoclaving
Here the horizontal slices should be carefully separated from the vertical slices before autoclaving and a gap should be created between the layers. This innovation eliminates any adhesion and speeds up the autoclave process because steam can penetrate the block faster.
After separating the, they enter the autoclaves during the cooking stage. The heat temperature inside the autoclaves is around 190-200 degrees Celsius and the pressure exerted on them is 12 atmospheres. The time required for baking is 10-12 hours, although the hardening time depends on the density and characteristics of AAC aerated concrete. At this pressure and temperature, the blocks are cooked and processed and the AAC block is produced. The whole process is automatic and AAC blocks are steamed safely.
In this system, a high-capacity steam boiler is needed to supply the steam needed by the autoclaves. After the cooking stage of the is finished, the final product is transferred to the dock and supply department to enter the consumer market. AAC block produced in this way will be very safe and strong, and it will be a good insulator for moisture, cold and heat, as well as sound.
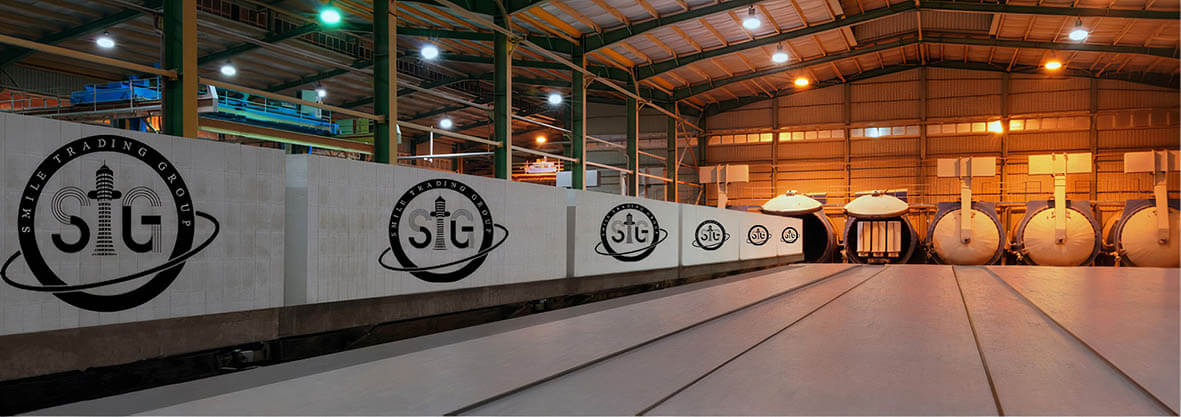
AAC block transmission device
The block transfer machine transports the cut blocks from the conveyor and places them on the wooden pallet provided by a block pallet. If the blocks are cut to different sizes in the cutting machine, the machine The block transfer is able to sort the blocks, so that each size model is packed separately.
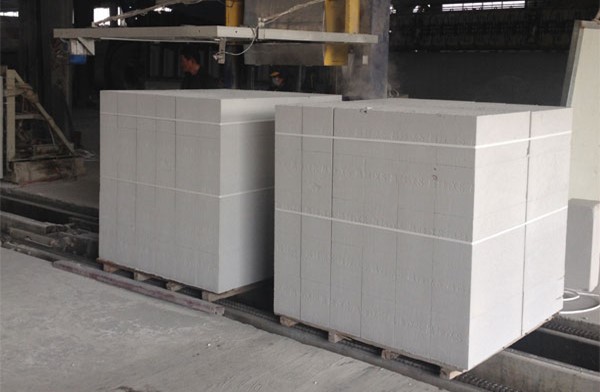
AAC block packaging
High quality concrete blocks need convenient and fast packing. Therefore, the finished product must be packaged and protected from dirt and moisture before leaving the factory. AAC block packing process can be done automatically or semi-automatically. The transport pallet filled with blocks should preferably be secured with plastic straps for transport and storage.
Reasons for the Use of AAC Lightweight Concrete Blocks in the World and Europe
Nowadays, new products are hitting the lightweight construction materials market, among which the standout is AAC lightweight concrete or AAC blocks. The unique characteristics of AAC blocks, a type of autoclaved lightweight concrete, have led to a warm reception from European and American companies towards these materials. Currently, in Europe, autoclaved blocks are being used in large-scale projects. AAC autoclaved lightweight concrete is recognized globally as a green product for construction. This product offers the best thermal insulation, weight, and strength ratios among all hard construction materials.
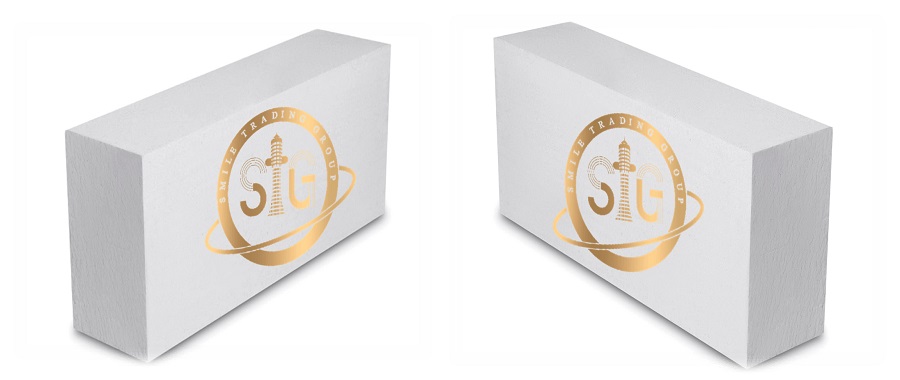
Attractive and wonderful features that are exclusive to AAC blocks.
It increases the construction speed by 3 to 4 times ompared to normal materials.
It is cost-effective and also reduces steel consumption by more than 30%.
It is very light building reduces the static load of tall buildings and towers.
It is very light weight with a density of 450 to 550 kg/m2 (one third lighter than normal materials)
It reduces construction costs and saves time.
It does not need wall post.
Sound insulation exceeding 50 decibels.
Thermal and cooling insulation, significantly reducing energy consumption heating and cooling compared to conventional building materials
Moisture insulation and freeze resistance.
Cost savings and ease of transportation due to the ability for palletized packaging.
Remarkably fast and easy installation owing to lightweight, precise sizing, impact resistance and screw-compatibility.
Easy cutting for carrying out electrical and plumbing installations.
A fire-resistant wall capable of withstanding direct fire up to 1200 degrees Celsius for 4 hours.
Reduction of earthquake forces due to low density, decreased dead load of the structure, and high compressive strength.
15. High safety and durability without the need for repairs.
Minimal finishing coverings for façades, leading to reduced plastering costs due to a smooth and level surface.
Increase in interior space of the building
Production capability based on client needs
No penetration of vermin
Recyclable and non-toxic
Environmentally friendly and compatible
Standard surface water absorption at the initial 1 centimetre, with proper adhesion of façade coverings
It does not submerge in water for up to 6 months
Resistant to loads caused by strong winds and storms
Known as lightweight concrete, composed of silica, cement, lime, aluminium powder, stone gypsum, and water.
Unlike conventional hollow materials, this material has a dense, porous, and white appearance.
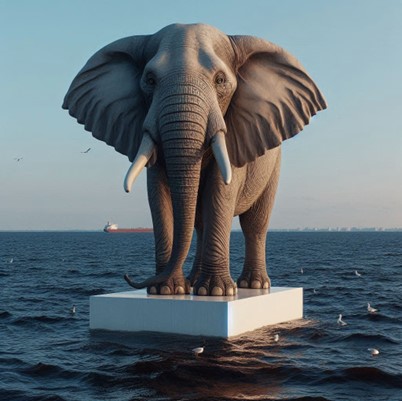
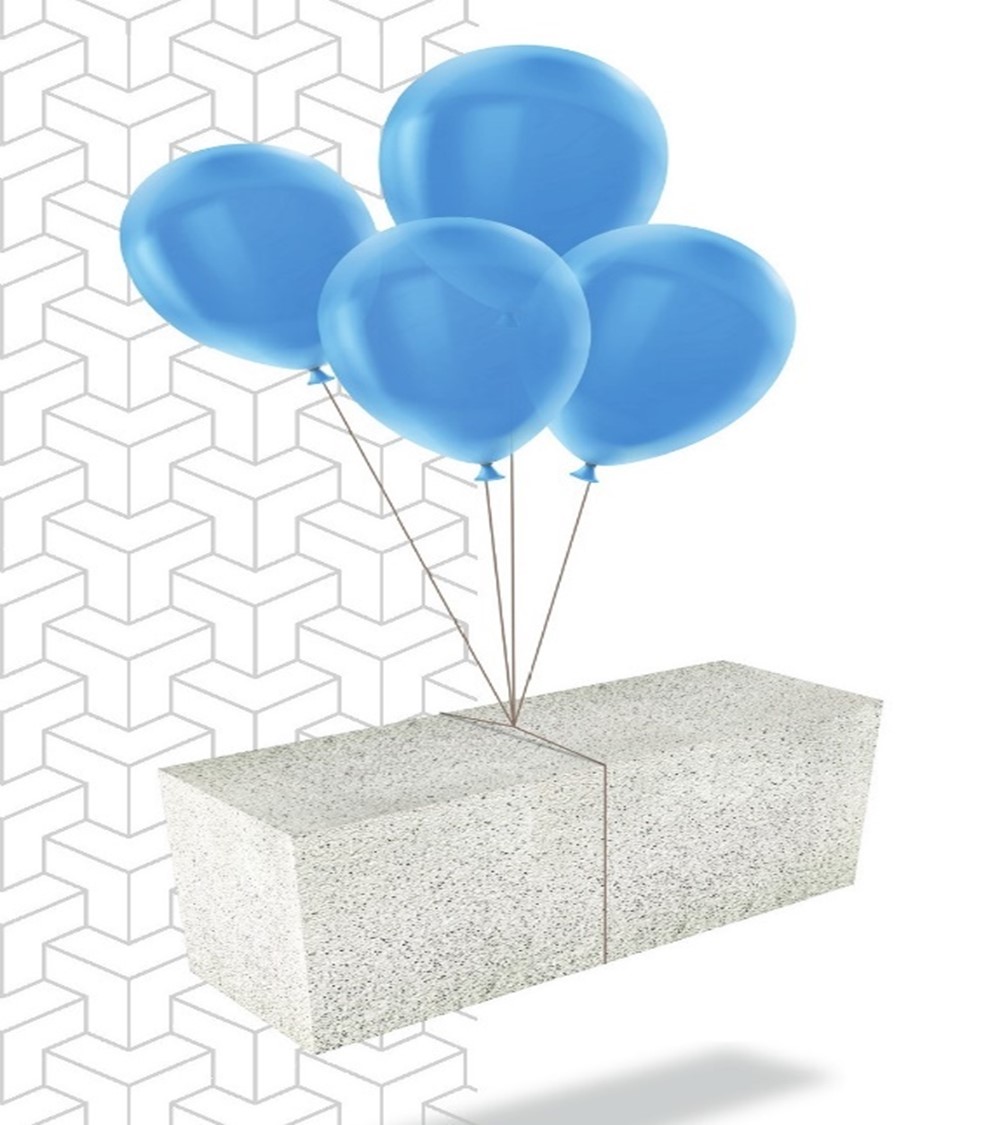
Light in Weight
Autoclaved lightweight concrete has millions of air bubbles in it. Right now, the lightest building materials in the masonry sector are lightweight STG concretes, with a production density of 450 to 550 kilograms per square meter. Compared to similar materials, it is on average 45% lighter, which means in designing structural members, there's at least a 10% saving in concrete or iron materials due to reduced dead load.
STG blocks, with their unique structure, require very little maintenance and renovation for a long time and have a notably long lifespan. They are also quite durable. The speed of laying these blocks is three times that of other wall construction materials due to their light weight and dimensions.
Additionally, it saves 25% on mortar usage and has a 30% cost saving. One reason for the lightness of STG blocks is that 80% of the air inside the initial mortar is retained.

Reduction Of Earthquake Force
With the low density and reduced dead load of light STG concrete, according to Iran's standard 2800, fourth edition, we will see favorable results in reducing the effective seismic weight of structures. As a result, the earthquake shear force, known as base shear, can be easily reduced by up to 10%. Consequently, the less base shear structures have, the better their seismic performance will be during an earthquake.
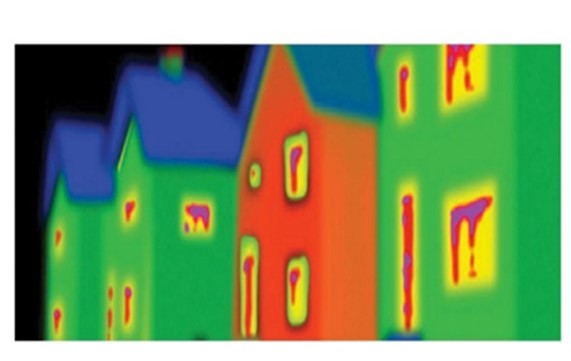
Thermal Insulation
According to building regulations, the exterior walls of the building must have proper insulation against cold and heat throughout different seasons. Unfortunately, in some countries, over 30% of energy loss comes from these building walls, which can be easily observed through thermographic testing. The STG lightweight block is the only wall construction product that can be implemented with a heat transfer coefficient of 0.11 watts per meter Kelvin without any thermal details; and we’ll have a building that’s up to 70% more insulated. In contrast, similar clay, concrete, and even cement blocks require thermal insulation to be applied on them, and the main reason for this insulation capability of STG blocks is their homogeneous structure in all directions, which is not found in any of the similar materials. In the image below, the green color represents energy-efficient buildings, while the red color indicates high-consumption buildings.
Thermal insulation provides:
1- Energy savings and a noticeable reduction in costs.
2- A comfortable temperature inside the building during the very cold winter months and also in extremely hot summer conditions.
3- A calm, safe, and moderate environment against climate changes.
4- Reducing energy consumption not only saves money but also prevents heat loss and its release into the atmosphere, ultimately contributing to global warming.
5- Savings and reductions in volume, number, and equipment needed for cooling and heating by approximately 45%.
6- With the use of this block, there’s no longer a need for thermal coverings in the building. It effectively and significantly reduces heat and cold transfer from one environment to another.
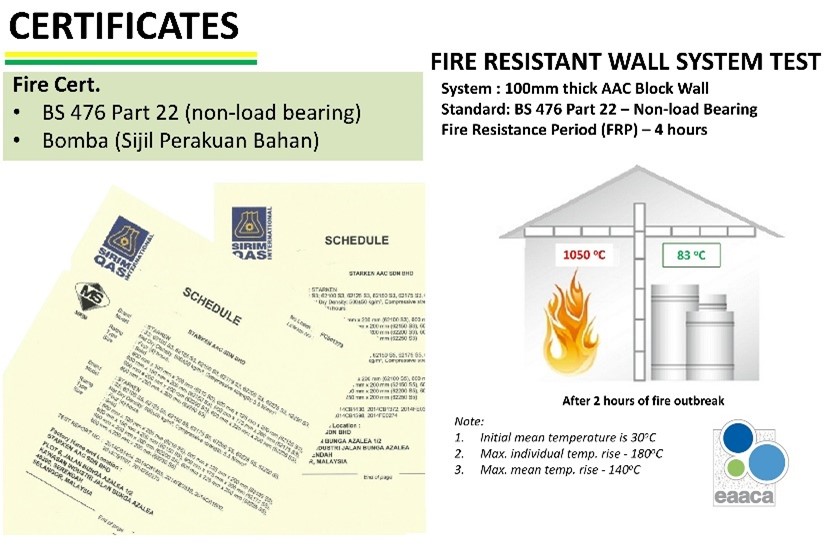
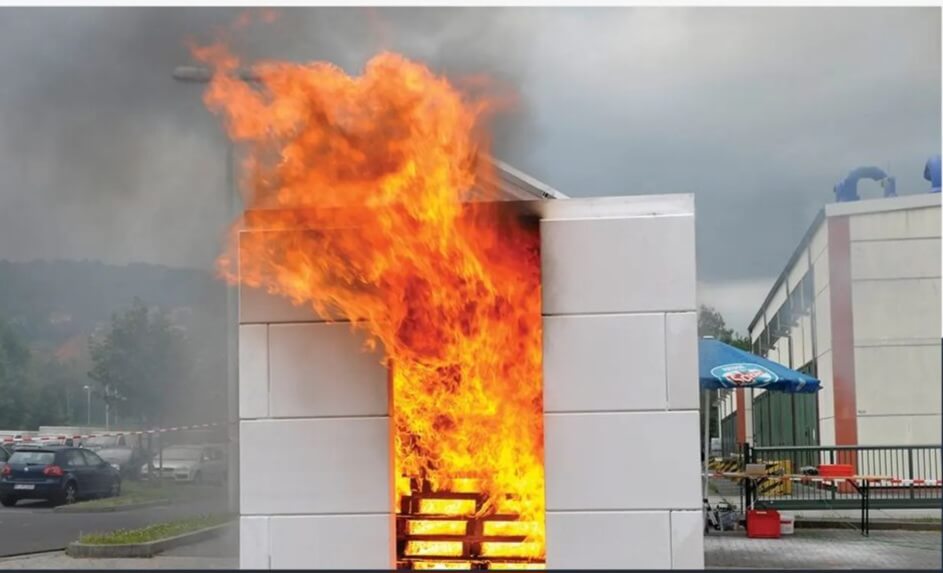
Fire Resistance
The autoclaved lightweight concrete STG is the first building material in the wall construction sector that has received a fire-resistance certification with the minimal wall thickness of 10 centimeters equivalent to the E120 rating from Iran's Road and Housing Research Center. According to the third section of Iran's national building regulations, fire safety at points of formation and preventing its spread is crucial for protecting human lives and investments. A test was conducted with STG blocks exposed to a temperature of 1200 degrees Celsius. A thermometer continuously monitored the temperature on both sides. On the other side of the wall, there was no noticeable temperature increase for two hours, and after four hours, the temperature only rose to 75 degrees. After the flame was extinguished, the wall remained intact and completely unharmed with no cracks. One of the toughest building standards is the fire-resistance rating (UL), which measures how many hours a material can withstand standard fire; this is a significant factor in preventing energy loss and provides thermal insulation. One of the main reasons for its high fire resistance is the use of non-flammable raw materials, including silica, which is included in the composition of these blocks, making them highly heat resistant. Moreover, this product does not emit any harmful gases in a fire.
This feature is particularly useful in sensitive and important public places like hotels, hospitals, educational institutions, libraries, and offices. Based on tests and evaluations conducted by the Research Center for Housing and Urban Development, the STG block, made from AAC blocks, has been assessed as 100 percent non-flammable.
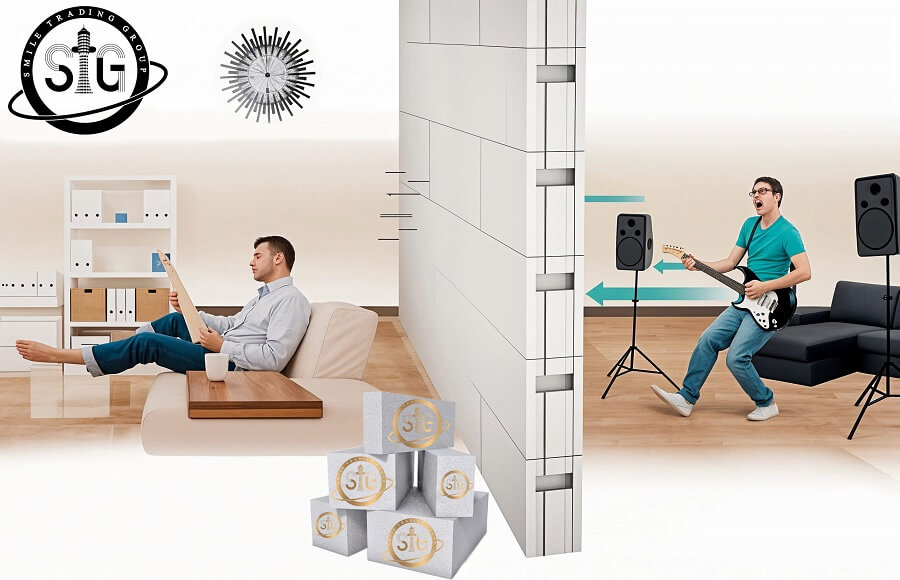
Sound Insulation
According to Topic 18 of the National Building Regulations, the optimal level of noise in different parts of each building is different from each other, and usually in residential buildings, the entry of more than 50 decibels of disturbing noise into the buildings will cause damage to the hearing system and reduce human comfort. The most common noises include ground and air traffic. In STG blocks, due to the impact of the sound wave with the porous surface of the block and their aerial particles, the wave movement is abrasive friction and as a result, the volume of sound movement is reduced. In fact, the pores of the sound-absorbing block are in a desirable way. STG blocks will have an average noise reduction of 45 to 50 decibels depending on the thickness of the wall design. This product has been able to achieve the ASTM standard in the category of very good insulators by greatly reducing the sound intensity and being insulated.
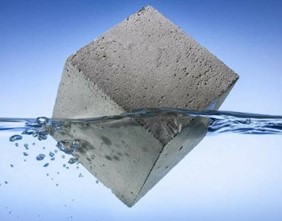
Waterproofing
The types of insulation of STG blocks have made it one of the best-selling materials of the day. One of the most important advantages of STG blocks is moisture insulation, and this product can be easily used in areas where the amount of moisture is very high and prevents moisture from penetrating into the house, and also in areas where heavy rains fall, this product is a very good insulation.
In the event of a break or crack in the water pipes in the building, the STG blocks play the role of insulation, causing the very place where the pipe break occurred, which will not be a cause for concern if it is prevented quickly. Finding the location of the burst in the houses made of this product is easy. STG blocks have been able to obtain the British standard number BS4315 as a waterproofing system.
STG blocks have standard surface water absorption within the initial 1 cm, with good adhesion for façade coatings, which does not submerge in water for up to 6 months.
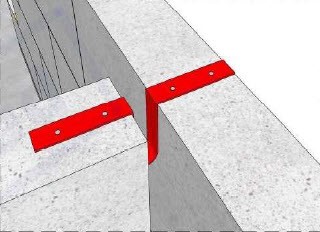
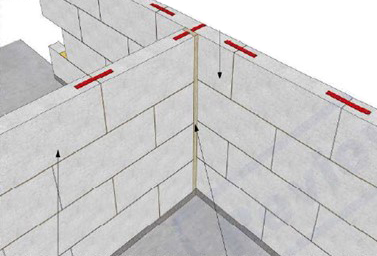
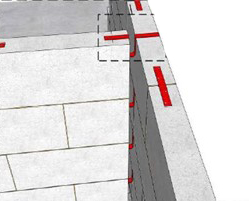
Wall post
According to Appendix VI of Standard 2800 of the Fourth Edition of Iran, STG light blocks do not need to be applied with substrate mortar, which is known as block adhesive, and will be replaced by simple steel or galvanized fasteners. In addition to increasing the speed of wall containment, we will see a reduction in the desired costs of at least 30% compared to the implementation of bed rebar. In STG blocks, due to their physical properties, the easy use of elastic fasteners known as radical or gonia packs is allowed and possible.
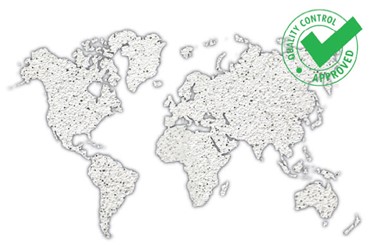
ECO Friendly
In the production of STG blocks, unlike other similar products, soil is not used, which is the most important source of human life, and we do not see the extraction and extraction of natural soils. In the production of this product, we have the least fossil energy such as gases, while in the production of other building wall products, we have a high percentage of energy waste due to production. STG autoclaved lightweight concrete is known as a green product for construction in the world. This product has the best thermal insulation, weight and strength ratios among all hard building materials.
Ordinary building materials create a large volume of construction waste. In addition to wasting money and time, it damages the environment and is almost unrecyclable. In addition to the blocks, they do not produce construction waste, but can be recycled. And it does not harm the environment. And by reducing the consumption of fuel and energy for cooling and heating the building, it prevents air pollution to a great extent.
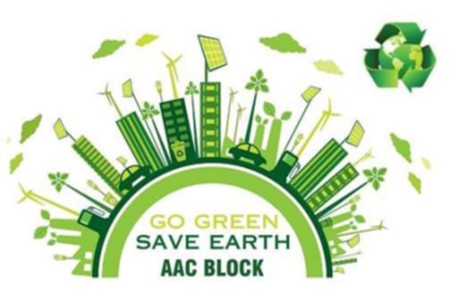
It is not corruptible
Firstly, due to the raw materials, this product cannot spoil and has a long shelf life. Secondly, because inorganic materials have been used to produce this product, it does not have any changes in nature and properties.
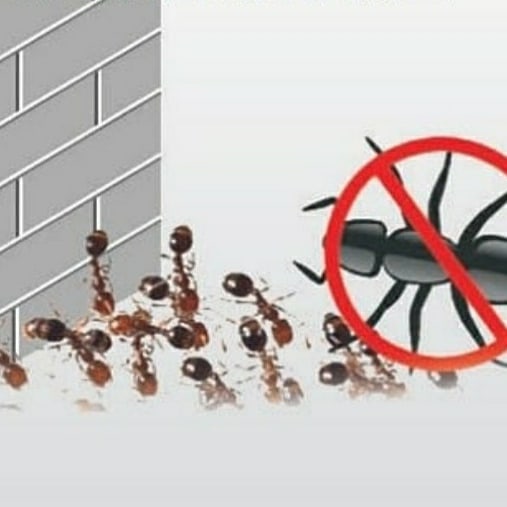
Termite Free
Due to the raw materials and inorganic and mineral structure, as well as the presence of empty space in STG blocks, no insects such as termites, ants, and beetles nest or lay eggs in it, and it is not possible for insects to penetrate this product. Mold and microorganisms do not form on or inside it. We will not have corrosion in them. It prevents pollution and penetration of insects and animals into the building and makes the structure safer.
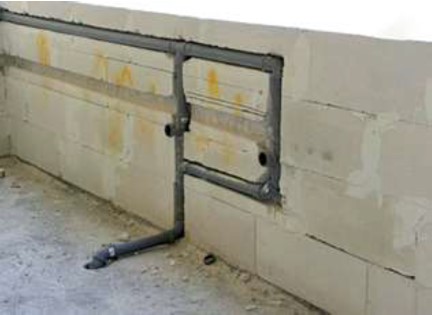
Groove and implementation of easy installations and minimal final coatings
STG blocks are completely solid while being lightweight. This feature has made grooving and grooving on these walls easier, and it will be easy to implement plans of electrical, mechanical, water and sewage installations on the wall. Also, due to the appropriate level and alignment of the walls executed with STG blocks, there is no need for the conventional implementation of gypsum and soil or thick cement plaster. The application of service coatings such as ceramic tiles is easily possible with thin-film adhesives, and façade coatings, which are known as plasters, with thicknesses of 1 to 3 mm, are easily possible. All of these factors increase the speed of construction up to 3 times compared to ordinary materials.
STG blocks can be easily sawn, nailed, drilled and grooved, which can significantly improve the construction speed and reduce cost and waste in the building.
In the table below, a comparison of the amount of implementation of different walls in square meters by a Materials Thickness implementation team

Standard water absorption and proper connection of façade coatings
Perhaps the concern about the rumor of non-adhesion and water absorption on the top of AAC blocks has been a concern of some community executives and engineers. According to the tests conducted on AAC light concrete and block concrete products, we will not have much difference in the adhesion of all types of stone and mortar. Also, regarding the issue of water absorption in accordance with the national standard of Iran, the standard absorption in the volumetric state of the blocks has been considered, which in all products water absorption is between 50 and 55 percent, and there will be no difference between this block and clay and cement blocks.
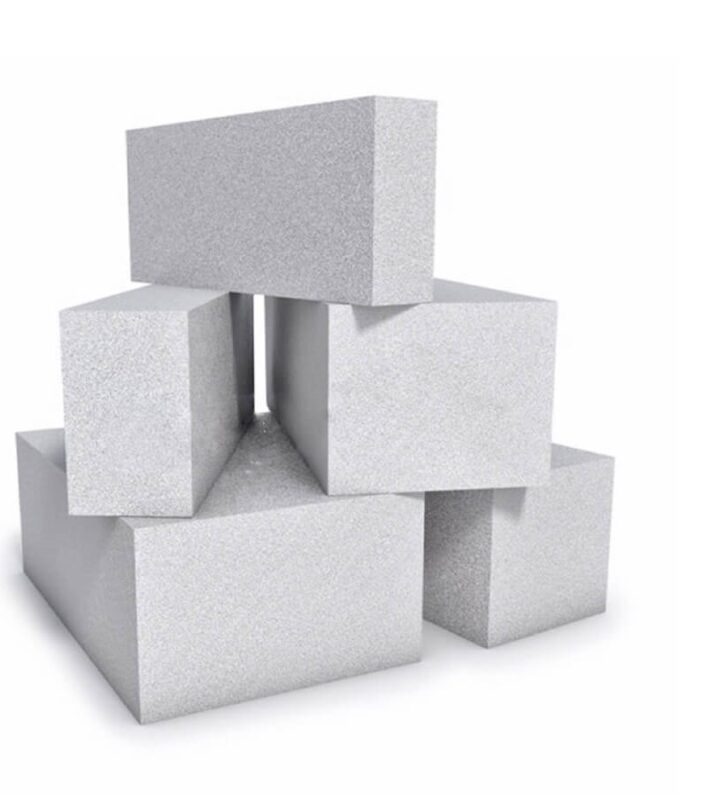
Frost Resistant:
STG blocks have good frost resistance due to their porous structure with a high percentage of closed cavities, which has passed its test in cold countries such as Sweden.

Cost-effective
According to the above contents, it is easy to understand how much construction costs as well as energy are saved. It should be noted that due to the elimination of costs such as substrate rebar, wall posts, no need for rabbit work, no need for thermal coating and moisture insulation, reduction of execution time, reduction of labor cost due to ease and speed in transportation and implementation, as well as reduction of material distractions, the use of STG block is very cost-effective.
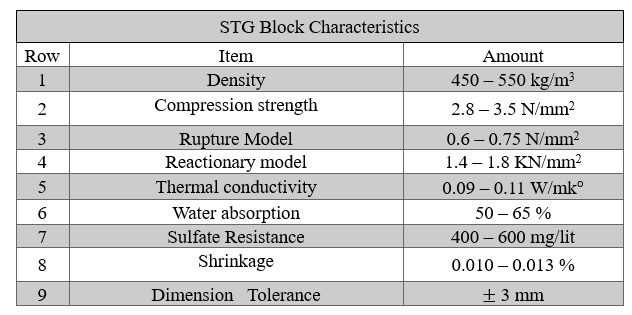
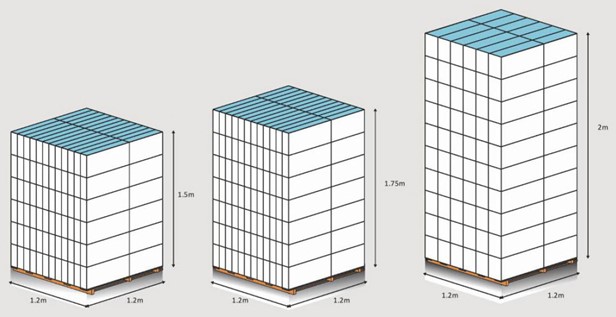
Pallet No. 1 with dimensions (1.2*1.2*2) is for export
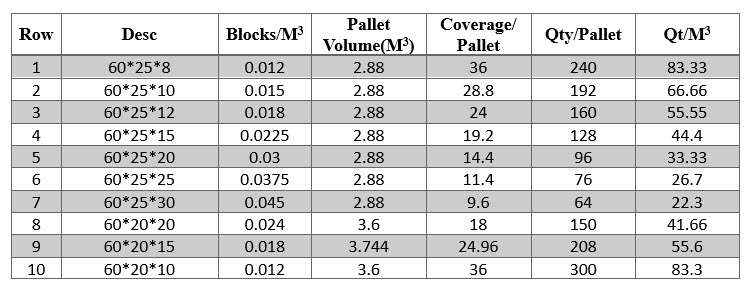

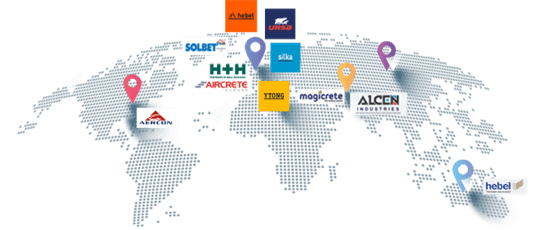
Famous Manufacturers Worldwide
Major manufacturers of light block are located in Europe, Asia, America, and Oceania, respectively. Also, two associations, AACPA (American AAC Association) and EAAC (European AAC Association), have been established in order to support the production and promotion of AAC in Europe and the Americas.
AAC light block is a successful example of mass construction and industrial construction in the UAE, Turkey and China in the last decade. And at environmental scientific conferences in Europe and the United States, the AAC block was introduced as a green material.
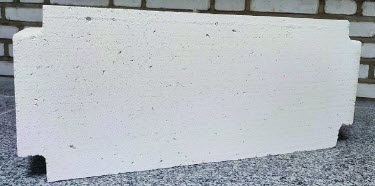
STG Ceiling Block
Roof block is one of the advanced and new building materials products, which is an excellent alternative to ordinary materials for the implementation of structural roofs. Due to its many advantages, this roof block has been very welcomed by engineers and project executors and has gained a lot of popularity, which is widely used in the construction industry. This product is produced in standard and specific dimensions. In terms of material and production stages, it is no different from the STG light block, and the only type of cut is different, and it is suitable for the ceiling, and it has all the advantages of STG light blocks, and because of its tightness, it also prevents the percussion sound.
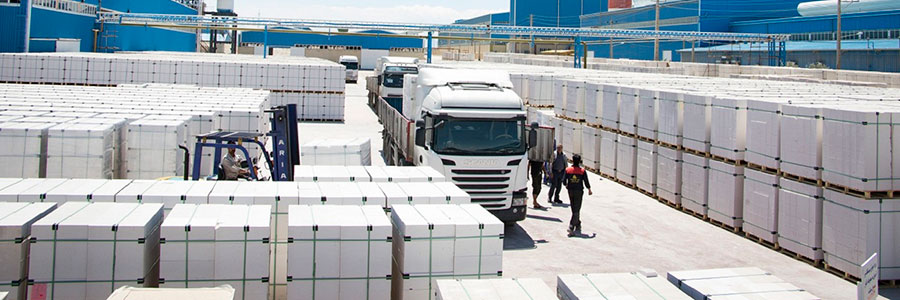
Guide to Maintenance and Implementation of STG Blocks
Maintenance
1- The unloading of the blocks should be done by a suitable means such as a forklift, and if the pallets are rubbed against each other, there is a possibility of damage and loss of corners.
2- The pallet of blocks and dry mortar should be unloaded and stored as close as possible to the project and on a flat surface above the ground.
3- If they are drained on the roof. It should be distributed near the columns and walls.
4- One day before using STG blocks, the coatings should be removed to make moisture and heat exchange with the environment. And at the end of each working day, it should be covered with nylon on the surface of the remaining blocks.
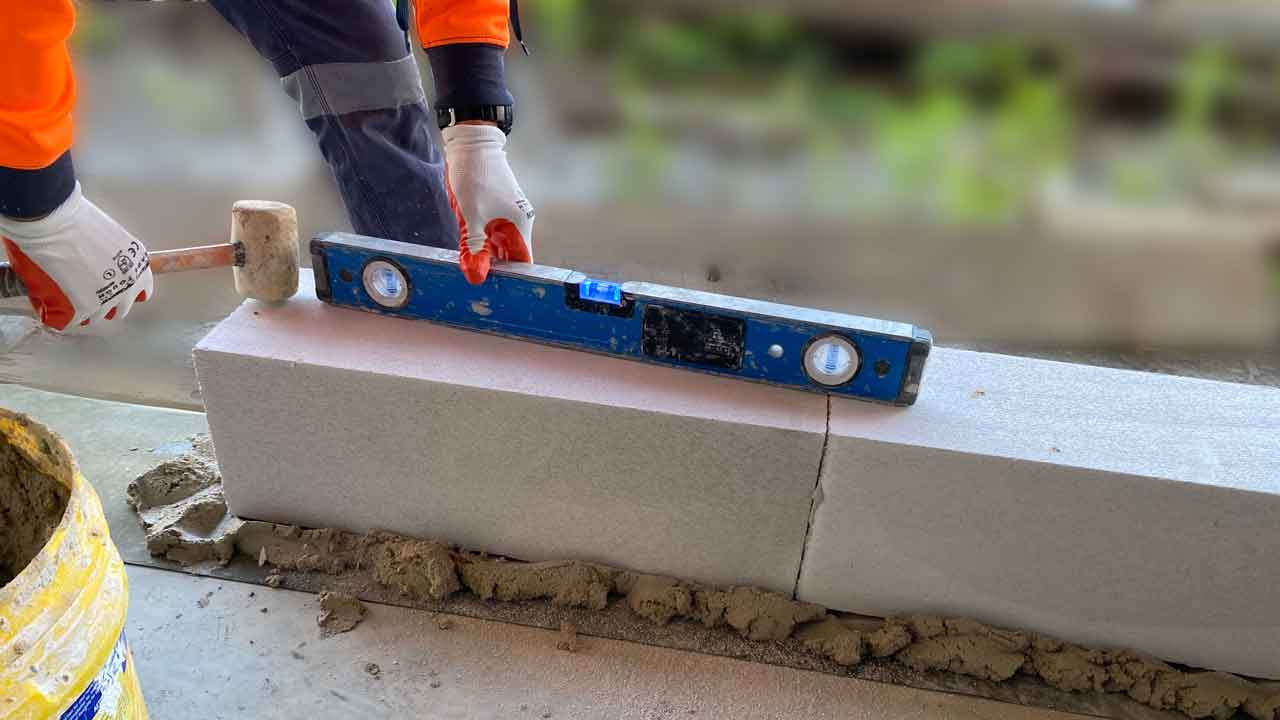
Installing First Row Blocks
1- The first row (first row) should be executed with precise control, alignment and direction.
2- The main extensions should be worked first, then the intersections.
3- Under the work at the site of laying the wall blocks using cement sand mortar, a smooth and level surface with a thickness of 1 to 2.5 cm should be created.
4- In the ground walls at a distance of less than 30 cm from the soil surface, a layer of moisture insulation should be applied before applying the mortar.
5- After each block is installed, its surface is cleaned with a brush, and then glued to the vertical surfaces of the block. The minimum thickness of the adhesive is 2 mm and the maximum is 3 mm. Before applying some water should be sprinkled on the surface
6- A trowel or a toothed spatula should be used to apply the glue.
7- After installing each block, check its levelness. Modifying with the slow strokes of the rubber hammer is possible in a maximum time of 5 minutes.
8- In order to prevent the inter-frame effect during the earthquake and the effects of expansion and contraction, the walls should be connected to the structure at a distance of at least one cm from the columns, beams, and concrete walls executed with flexible metal belts at a distance of up to three blocks (vertical and horizontal). For this purpose, perforated metal strips should be used at the junction of the side walls, seams and the connection to the column.
9- The distance and number of connecting tentacles should be controlled according to the height of the structure and the designer's opinion.
10- To fill the gaps, flexible materials such as polyportane, plastofoam, or dead plaster can be used.
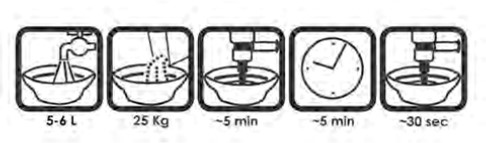
Preparation of Block Glue
The type of STG block adhesive or the related mortar must meet the requirements of the Iranian national standard No. 706. The STG block adhesive should be poured into suitable plastic containers according to the instructions on the envelope and mixed with clean water (drinking water). It is recommended to use a mechanized method for mixing and the disturbance continues until the air is removed. Therefore, for this purpose, a stirrer that is closed on the drill can be used and the mixing process can be continued at a low speed until the desired result is achieved.
The important point is that the efficiency life of mortars is known and generally between 4 and 5 hours. Thus, in the manufacture of mortar, care must be taken not to make additional mortar, in which case water cannot be added to it and reused after hardening.
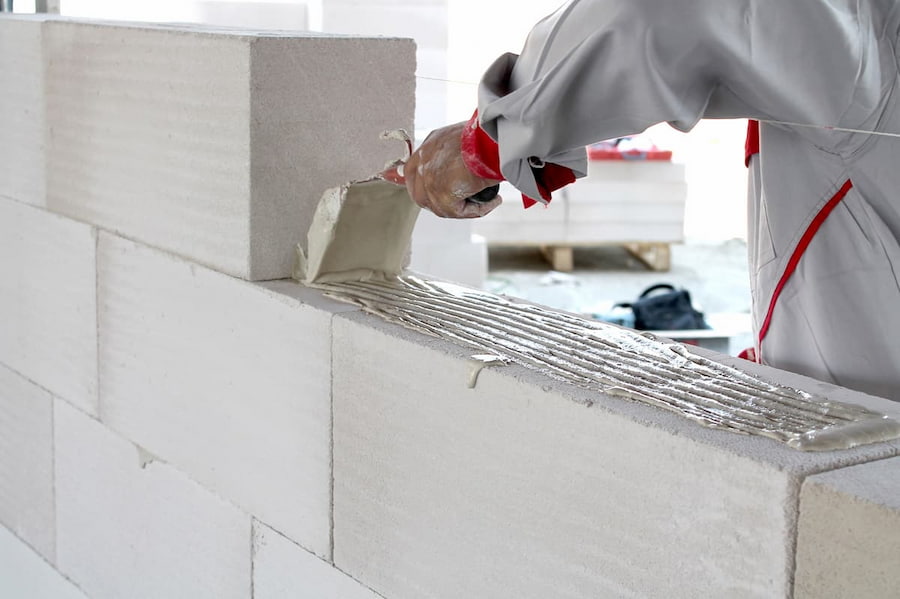
Installing blocks in the next row
At the time of implementation, the surface of the blocks should be wet. To implement the next blocks, the vertical and horizontal surfaces must be glued with a serrated trowel and the surface of the blocks must be cleaned with a brush before gluing.
When installing the block, first put the edge away from the block connection, and then the connecting part is in place. Avoid slipping the block and clean excess mortars with a spatula. The spatula should be placed 45 degrees relative to the block and the movement should be in such a way that the sharp edge is not towards the seam.
The overlap of blocks should be at least 5 cm (the minimum distance between vertical seams is 15 cm) and should be constant for each ridge (row).
At the angular intersection of the walls, the Persian surface should be placed on the outer side, in other words, the vertical seam should not be placed on top of each other, for the implementation of the wall work, the level and extension of each block should be controlled after installation.
The secondary wall with a thickness less than the main wall with an executive distance of about one centimeter and is connected to the main wall using steel strips with a distance of one meter.
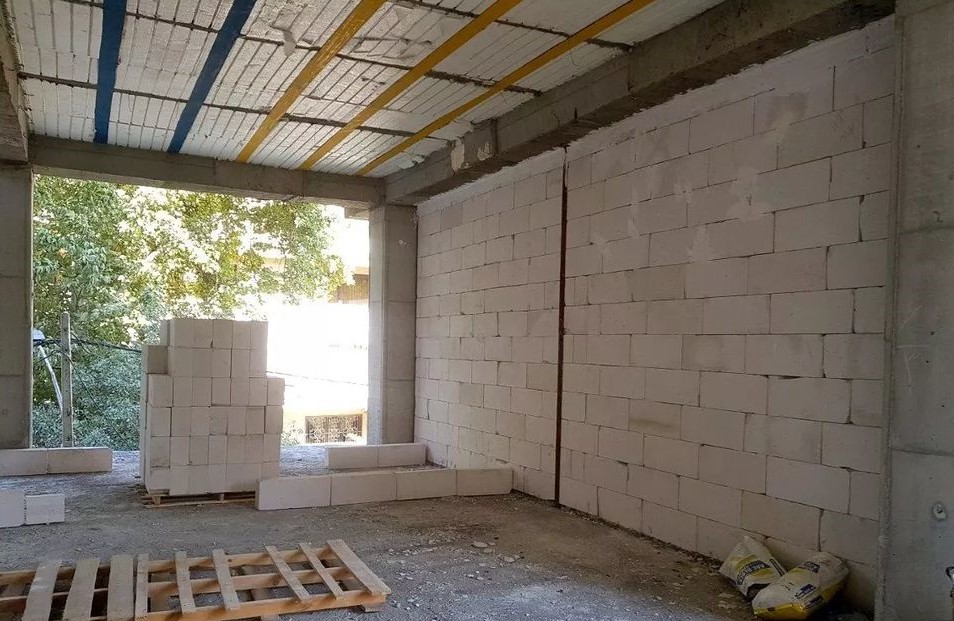
Backrest or coil
If the height of the wall is more than 3.5 meters, a horizontal coil attached to the structure of the building should be used. If the length of the wall is more than 6 meters or 40 times the thickness of the wall, it should be used as a backing strap or upright coil attached to the structure of the building. The vertical and horizontal edges of the blades should not be free.
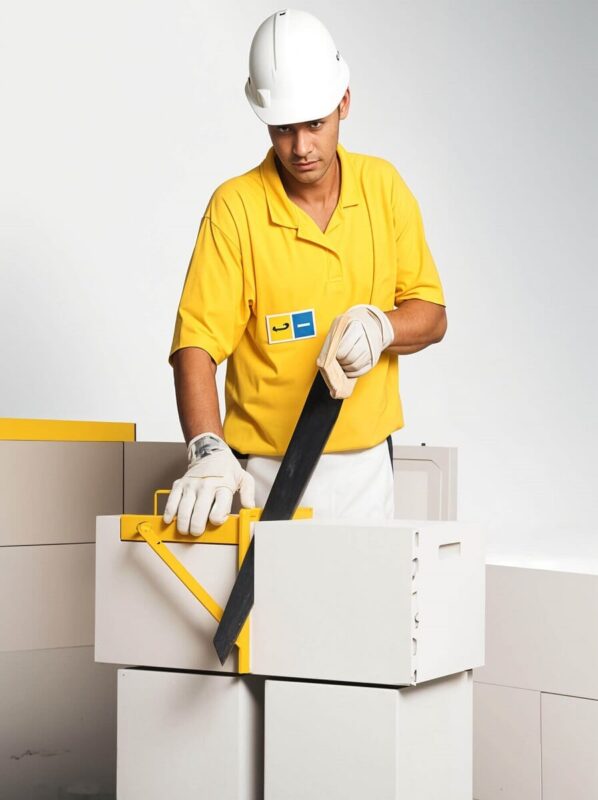
Cutting
Cutting can be done with hand saws, band saws, and woodworking tools in the desired dimensions and shape. In case of cutting with electrical appliances, use masks and safety supplies.
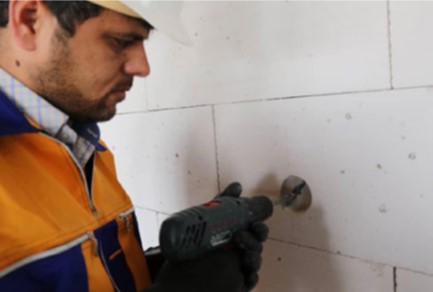
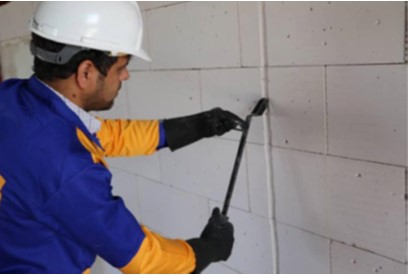
Drilling
Drilling should be done with a rotary cutting machine. The diameter of the hole should not exceed one-third of the depth of the block. Around larger holes should be reinforced with metal mesh. If the depth of the groove is more than one-third of the depth of the block, reinforcement should be done in both ridges with two 8 mm rebars.
Facilities Implementation
For the paths of the installations, vertical grooves and holes can be drilled in the walls. After the installation is implemented, additional paths and holes should be filled with block mortar adhesive.
Wall surface staining
Block mortar adhesive can be used to repair chipping and staining. Clean the surface with a brush before running. The staining is done using a spatula, then the surface is smoothed with a fine scraper or sander and ready to be painted.
Door & Window Installation
The installation of doors and windows is done directly on STG blocks, and it is better to use cement sand mortar for the placement of metal frames.
Joinery
With respect to the smooth surface, the wall can be covered by applying wallpaper, thin layer of plaster, cement plaster, ceramic, acrylic patterned coatings or ready-made mortar.
Before applying joinery and non-dry façade, the surface of the blocks should be thoroughly cleaned and then moistened.
In the place of discontinuity of walls, such as corners, next to openings, etc. fiberglass meshes can be used. The minimum curing time for plaster and surfaces that have been applied with cement sand mortar is three days, and the surface of the wall must be kept moist.
In the junction of different materials in the façade, such as the junction of the STG block with the reinforced concrete shear wall or the concrete and metal structure, rabbits (with the direction of the horizontal belt) should be used.
In industrial buildings and parking lots, STG blocks can be painted directly with acrylic paint.
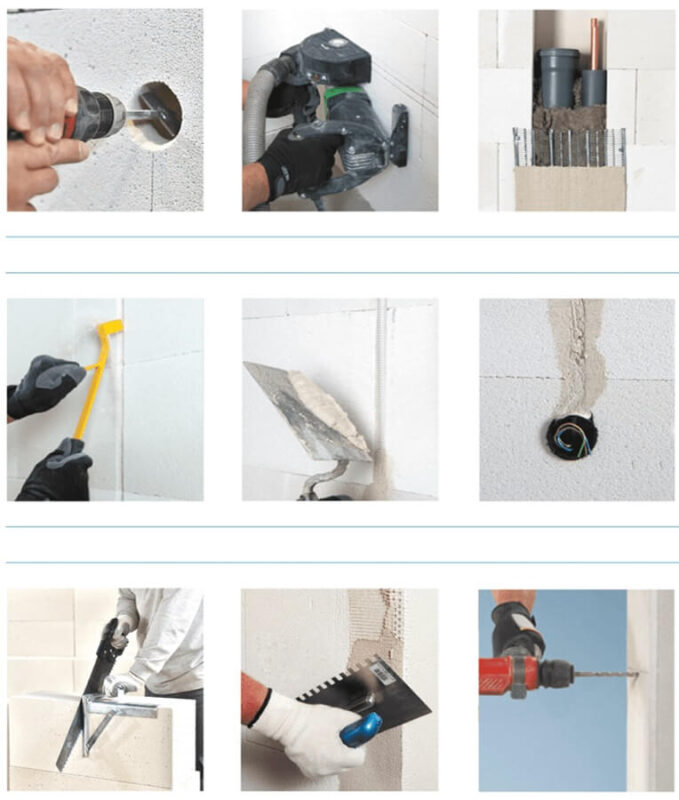
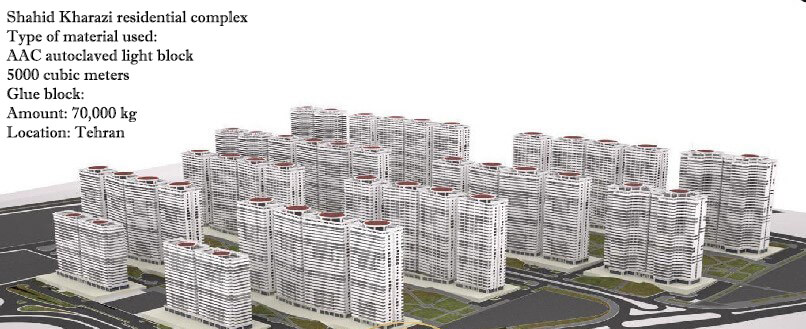
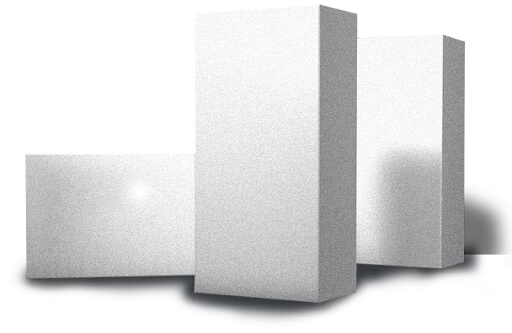